The Science Behind Porosity: A Comprehensive Overview for Welders and Fabricators
Comprehending the detailed systems behind porosity in welding is crucial for welders and fabricators pursuing impeccable craftsmanship. As metalworkers look into the midsts of this phenomenon, they uncover a world regulated by various aspects that influence the formation of these tiny spaces within welds. From the make-up of the base products to the complexities of the welding procedure itself, a wide range of variables conspire to either intensify or relieve the existence of porosity. In this extensive guide, we will untangle the scientific research behind porosity, discovering its results on weld quality and introduction progressed techniques for its control. Join us on this trip with the microcosm of welding flaws, where accuracy meets understanding in the search of perfect welds.
Comprehending Porosity in Welding
FIRST SENTENCE:
Exam of porosity in welding reveals important understandings right into the integrity and top quality of the weld joint. Porosity, characterized by the presence of cavities or spaces within the weld metal, is a typical worry in welding processes. These voids, otherwise effectively attended to, can jeopardize the architectural integrity and mechanical homes of the weld, resulting in prospective failings in the finished product.
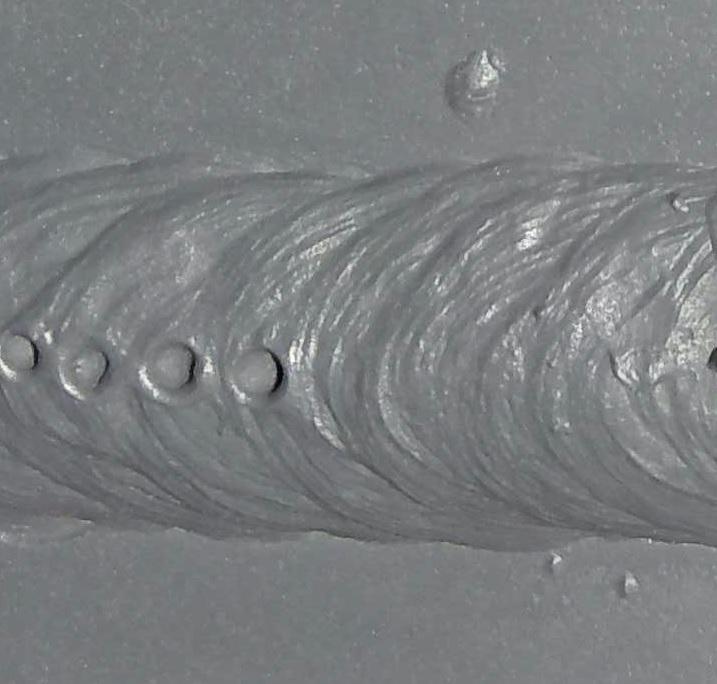
To identify and quantify porosity, non-destructive screening techniques such as ultrasonic testing or X-ray evaluation are usually used. These strategies permit the identification of inner flaws without compromising the integrity of the weld. By evaluating the dimension, shape, and circulation of porosity within a weld, welders can make informed decisions to boost their welding procedures and achieve sounder weld joints.
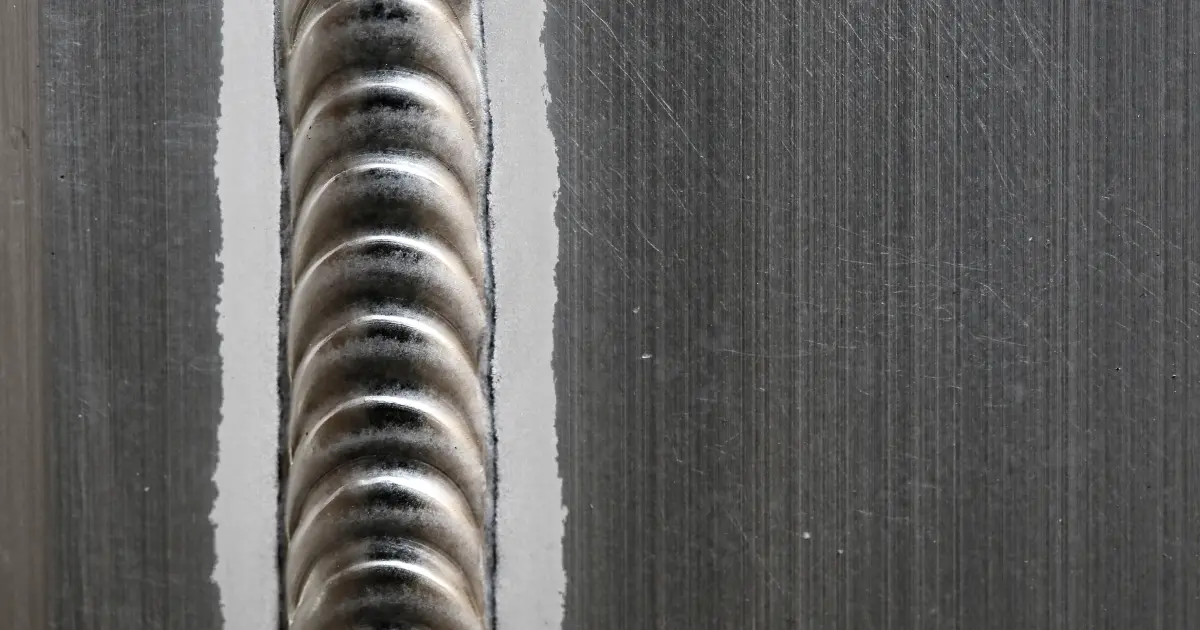
Elements Affecting Porosity Formation
The occurrence of porosity in welding is affected by a myriad of elements, varying from gas securing efficiency to the details of welding parameter setups. One important variable adding to porosity formation is inadequate gas protecting. When the protecting gas, normally argon or carbon dioxide, is not effectively covering the weld pool, climatic gases like oxygen and nitrogen can pollute the liquified metal, leading to porosity. In addition, the sanitation of the base materials plays a significant role. Impurities such as rust, oil, or wetness can evaporate throughout welding, developing gas pockets within the weld. Welding parameters, consisting of voltage, existing, take a trip rate, and electrode kind, likewise impact porosity formation. Making use of inappropriate setups can generate extreme spatter or heat input, which subsequently can lead to porosity. Additionally, the welding method utilized, such as gas metal arc welding (GMAW) or secured metal arc welding (SMAW), can affect porosity development because of variations in warmth circulation and gas coverage. Understanding and managing these elements are essential for reducing porosity in welding operations.
Effects of Porosity on Weld High Quality
Porosity formation considerably compromises the architectural honesty and mechanical residential or commercial properties of bonded joints. When porosity exists in a weld, it develops voids or cavities within the material, minimizing the general stamina of the joint. These gaps act as anxiety focus points, making the weld extra prone to splitting and failing under load. The visibility of porosity additionally damages the weld's resistance to rust, as the entraped air or gases within the voids can react with the surrounding setting, leading to deterioration gradually. In addition, porosity can impede the weld's ability to endure pressure or effect, more endangering the general quality and reliability of the bonded framework. In important applications such as aerospace, vehicle, or architectural building and constructions, where safety and security and sturdiness are critical, the damaging impacts of porosity on weld top quality can have serious consequences, stressing the importance of reducing porosity through correct welding techniques and procedures.
Techniques to Reduce Porosity
To boost the high quality of bonded joints and ensure architectural integrity, welders and fabricators employ specific techniques focused on minimizing the continue reading this development of voids and cavities within the product throughout the welding process. One efficient technique to decrease porosity is to make certain correct material preparation. This consists of detailed cleaning of the base metal to get rid of any kind of impurities such as oil, oil, or wetness that could add to porosity development. In addition, utilizing the suitable welding parameters, such as the proper voltage, current, and take a trip rate, is important in stopping porosity. Preserving a constant arc size and angle during welding also helps in reducing the probability of porosity.

Using the ideal welding method, such as back-stepping or utilizing a weaving activity, can likewise help distribute heat uniformly and reduce the possibilities of porosity formation. By carrying out these methods, welders can efficiently minimize porosity and produce top notch welded joints.
Advanced Solutions for Porosity Control
Implementing advanced technologies and ingenious techniques plays a pivotal role in attaining remarkable control over porosity in welding processes. One advanced option is the usage of innovative gas mixes. Securing gases like helium or a combination of argon and hydrogen can help in reducing porosity by supplying far better arc stability and boosted gas insurance coverage. Furthermore, employing advanced welding strategies such as pulsed MIG welding or customized ambience welding can also aid minimize porosity issues.
One more sophisticated solution involves using sophisticated welding devices. Using devices with built-in features like waveform control and advanced power sources can boost weld quality and decrease porosity risks. Additionally, the execution of automated welding systems with specific control over parameters can significantly reduce porosity defects.
Additionally, including sophisticated monitoring and examination innovations such as real-time X-ray imaging or automated ultrasonic testing can aid in discovering porosity early in the welding procedure, allowing for immediate corrective activities. Generally, incorporating these advanced solutions can substantially boost porosity control and boost the overall quality of bonded components.
Final Thought
Finally, comprehending the science behind porosity in welding is important for welders and fabricators to generate top quality welds. By recognizing the aspects affecting porosity development and implementing methods to decrease it, welders can improve the total weld top quality. Advanced services for porosity control can even more enhance the welding procedure and ensure a strong and trusted my company weld. It is very important learn the facts here now for welders to continuously inform themselves on porosity and apply finest practices to attain optimal results.
Comments on “Discover What is Porosity in Welding and Its Result on Structural Integrity”